- 2021-4-16
- 最新情報
- 3DFS, 3DPrinting, 3Dプリンティング, ABS, FDM, FFF, filament, Medical, PLACTIVE, SLS, テクノロジー, デザイン, バイオマテリアル, フィラメント, 仕上げ加工, 医療, 工業デザイン, 工業製品, 表面仕上げ
可動式金属ピンで構成された3Dプリンティングプラットフォームによりサポート構造を大幅に削減
南カリフォルニア大学とスイス連邦工科大学(EPFL)コンピュータ・コミュニケーション科学部の研究者等は、動的に制御された3Dプリンティングプラットフォームをベースとした低コストで再利用可能なサポート機構を開発。FDM(FFF)方式3Dプリントにおける材料の無駄を大幅に削減することに成功した。
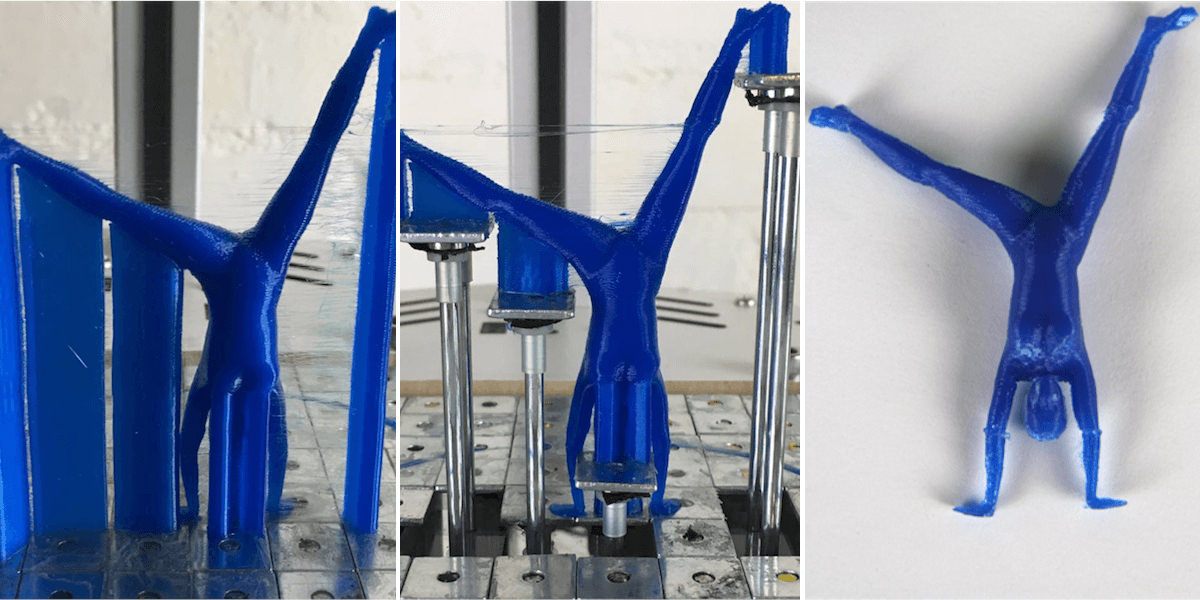
従来の押出し式3Dプリント方式では、張り出した構造や複雑構造を有するモデルを3Dプリントする際、モデルの破綻を防ぐため、サポート構造を組み込む必要がある。モデルを支えるために設けられるこのサポート構造により余分な材料が追加され、リードタイムが長くなるだけでなく、材料を大量に消費し、殆どの場合それらは廃棄物として処理されている。
研究チームが開発したこの装置は、ノズル式または押出し式の3Dプリント造形をサポートするために設計されたもので、3層のシートメタル構造の中に、動的に制御された複数の金属ピンが備えられており、最初の2層はデバイスの外枠に取り付けられ、3層目は3Dプリンタで制御される電動ステージに接続されている。この造形台は各層をプリントする際にプリントヘッドのレベルに合わせて上昇し、プリントを終えた造形物からサポート構造を除去してピンをリセットすることで、次のジョブとして再利用することができる。これにより、無駄なサポートが不要となり、信頼性の高い堅牢な構造体を約35%少ない材料で造形することが可能で、プリント時間も約38%短縮する。
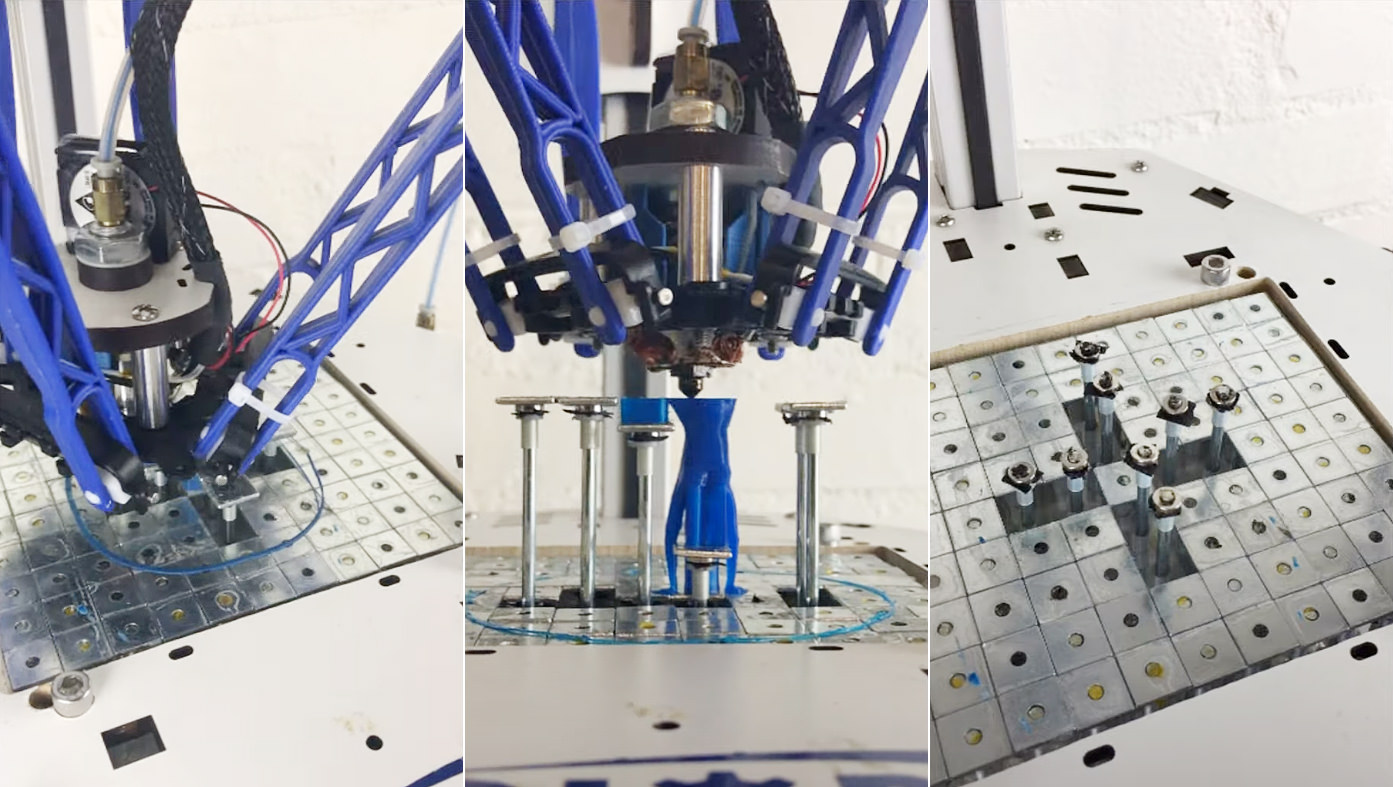
それぞれのピンが適切な高さになると、磁気ディスクとリングの組み合わせで固定され、プリントエラーになることを防ぐ。このサポート機構の効果を最大限に発揮させるため研究チームは、カスタムCADモデルとプロトタイプFDMシステム(Orion Delta ベース)を開発。プログラムのソフトウェアは、モデルの設計に基づいて、プラットフォームのベースに一連の金属チューブを追加する必要がある場所をユーザーに伝える。
このシステムを利用しABSとPLAのテストプリントを行った結果、15mm、30mm、45mm、60mmのオーバーハングのパーツを製作する際、追加のサポート構造を必要としなかった。またそれ以上のオーバーハングの場合でも、通常よりも大幅に少ないサポート構造でプリントできることを証明した。
過去に開発された同様のプロトタイプでは、それぞれのサポート構造を上昇させるため、個別のモーターを使用しており、仮に100本の可動ピンに対しそれぞれのモーターのコストが10ドル程度だとした場合、100個のモーターを制御するための25枚の制御基板と合わせ、1万ドルを超える可能性があり、費用対効果の低いシステムとなっていた。今回研究チームが開発したこの新しいシステムは、ひとつのモーターで同時に複数の金属ピンを持ち上げることができるため、費用対効果の高いソリューションとなっている。
研究チームによれば、このシステムは自動車、航空宇宙、ヨットなどの大規模な製造にも容易に適用することが可能で、特にバイオメディカルなど高価な材料を利用する3Dプリントにも適してるとしている。
組織や臓器を造るために生体材料を使うバイオ3Dプリンティングでは、使用する材料の多くが非常に高価で、1本500ドルから1000ドルもする小さなボトルを使用している。一般的な押出し式3Dプリンタで使用される材料と比べて非常に高価なため、無駄な材料として消費されるサポート構造を削減することで、バイオメディカル目的の3Dプリント時にとって大きなコスト削減に繋がる。
また将来的には、このシステムをSLA、SLM、DIWなど他の3Dプリント方式にも応用できると考えており、これを実現するため研究チームは、温度制御の改善やABSの反りの低減を可能にする密閉型のチャンバーなど、将来のアップグレードに取り組んでいる。
関連記事
- ストラタシス、粉末ベースの3Dプリント技術を発表
- Snapmaker 2.0 ロータリーモジュール
- 安価で高性能なセラミック3Dプリンタ「Cerambot Eazao」
- 製造を効率化させるAIソフトウェア「Blacksmith」
- Stratasys、3DプリンタメーカーRPSを買収
- ストラタシス「Origin」を1億ドルで買収
- Flashforge 3Dプリンター「値下げ」のお知らせ!
- フォルクスワーゲン、3Dプリンタ導入で設計強化
- アルファロメオ新型F1マシンに143個の3Dプリントパーツを装備
- 12個のレーザーを搭載したメタル3Dプリンタ「NXG XII 600」
- BMWが大規模な3Dプリンティングキャンパスを開設
- AMレーザー収益が2024年までに8億7,000万ドルに達する
- HPは過去1年で1000万点以上の3Dプリント部品を製造
- BMWは3Dプリント技術で100万個超の自動車部品を製造
- 導電性フレキシブルTPUフィラメント「Conductive Filaflex」
- 100%リサイクルされたTPUフィラメント「Reciflex」
- ステンレス鋼部品製作用「Ultrafuse 316L」販売開始
3DP id.arts の最新投稿をお届けする「Newsletter 3DP id.arts」への登録はこちら
最新情報をお届けします
Twitter でid.artsをフォローしよう!
Follow @idarts_jp